Published Date
Author
1. Introduction
Most commercially produced composites use a polymer matrix material often called a resin solution. There are many different polymers available depending upon the starting raw ingredients. There are several broad categories, each with numerous variations. The most common are known as polyester, vinyl ester, epoxy, phenolic, polyamide, polypropylene, polyether ether ketone (PEEK) and others. Polymer matrix composites are very popular due to their low cost and simple fabrication methods. Reinforcement of polymers by strong fibrous network permits fabrication of PMCs [1].
A particle by definition is non-fibrous and generally has no long dimension. The dimensions are approximately equal in all directions. The shape of the reinforcing particle may be spherical, cubic, platelet or any regular or irregular geometry. The arrangement of the particulate reinforcement may be random or with preferred orientation. Particles are effective in enhancing the stiffness of composites. The particles and matrix material in any particulate composites can be any combination of metallic and non-metallic materials [2]. Particulate fillers modify the physical and mechanical properties of polymers in many ways. The mechanical properties of particulate–polymer composites depend strongly on the particle size, particle–matrix interface adhesion and particle loading [3].
Coconut shell is one of the most important natural fillers produced in tropical countries. It is a natural lignocellulose material and possesses the distinctive characteristics that add to the versatility leading to diverse end uses such as- renewable resource, non toxic in nature, biodegradable, low density, low cost, easy availability and good durability [4]. Many works have been devoted to use of other natural fillers in composites in the recent past and coconut shell filler is a potential candidate for the development of new composites because of its high strength and modulus properties. Composites of high strength coconut filler can be used in the broad range of applications such as building materials, marine cordage, fishnets, furniture and other household appliances [5].
Physical aging is generally characterized by increase in mass density (volumetric relaxation) and/or decrease in molecular configurational energy (enthalpy relaxation) of materials when exposed to temperatures below the transition temperature [6].
2. Materials and Manufacturing
The raw materials used in this work are Coconut Shell Grains, Epoxy Resin (LY556), Hardener (HY951) and Melamine. Coconut shell grains were produced by crushing the coconut shells which is the most versatile part of the coconut. The shell is organic in nature and also has good durability characteristics, high toughness and abrasion resistant properties. The shell is similar to hard woods in chemical composition though lignin content is higher and cellulose content is lower. Advantages of natural fibers include low specific weight, which results in a higher specific strength and stiffness than glass. This is a benefit especially in parts designed for bending stiffness. Furthermore, it is a renewable resource, the production requires little energy and carbon dioxide is used while oxygen is given back to the atmosphere.
The shells of fully matured coconuts were first cleaned and crushed into smaller grains as shown in Fig. 2. These smaller grains were then subjected to repeated grinding in pulverizing machine, after passing through cyclones and vibratory sieves fitted with phosphor-bronze mesh, grains are finally drawn out in different mesh sizes.
2.1 Sieving Process
In this process, the coconut shell grains were sieved in to different grain sizes of 0.25 mm, 0.5 mm, 1mm and 2mm through the metallic sieves as shown in Fig. 3.
Open mould process was used to produce the composites. Initially the coconut shell particles of required grain sizes were weighed in a weighing machine, and then the required amount of epoxy resin, hardener and melamine powder were mixed with these grains and composites were produced.
The composite boards were prepared according to the following steps
Step 1: Appropriate volume of coconut shell particles and epoxy resin were taken in a plastic container and stirred thoroughly to make a homogeneous mixture. After adding 10% of hardener and 5% of melamine powder, the mixture was again stirred for 10 minutes.
Step 2: Open moulds used in this process were made from bright rod. Each mould has a cavity to accommodate the composite samples. The dimensions and shapes of cavities were made according to ASTM standards and thoroughly mixed mixture was poured in the mould.
Step 3: The composite samples were produced for different grain sizes of 0.25 mm, 0.5 mm, 1 mm and 2 mm.
2.2 Flexural Test Specimens
Flexural strength is the ability of the composite material to withstand bending forces applied perpendicular to its longitudinal axis. Flexural test can be performed using 3-point bending method according to ASTM D790-03 standard procedure. The specimens are tested at a crosshead speed of 0.5 mm/min. The value of gauge length (L), width (d) and thickness (h) of the test specimen used in the experimentation are to be considered.
The specimens were prepared according to the ASTM D790-03 [7] with dimensions of the specimen in millimeter as 200 x 12 x 12 and the span length as 160 mm as shown in Fig. 5.
3. Experimentation
Accelerated aging is defined as the process or processes required to accelerate a specific mechanism or mechanisms relative to a baseline aging condition [8]. The specimens were subjected to accelerated ageing by hot boiling. Three sets of specimens of different grain sizes of 0.25 mm, 0.5 mm, 1 mm and 2 mm for different filler / resin weight proportions of 40:60, 50:50 and 60:40 respectively were boiled for three hours at different temperatures of 40 °C, 60 °C and 80 °C respectively for each set and then dried in the Oven for three hours at a temperature of 60 °C as shown in Fig. 6 [9].
The flexural strength is calculated by [7, 10],
The flexural modulus is determined by [7, 10],
where,
P is maximum load in Newton
L is span length = 160 mm
b is width of specimen = 12 mm
h is thickness of specimen = 12 mm
m is slope of linear portion in load v/s deflection graph
The Flexural test was carried out in Universal Testing Machine (UTM) interfaced with deflectometer attachment as shown in the Fig. 7.
4. Results and Discussion
The flexural strength and flexural modulus obtained for the specimens boiled at different temperatures are discussed below.
Load v/s Deflection curves for the specimens boiled at 40 °C are as shown in Figures 8, 9 and 10.
From Fig. 8, it can be observed that the specimen with 0.25 mm grain size and 40:60 weight proportions sustains a maximum load of 271.47 N with deflection of 4.3 mm.
From Fig. 9, it can be observed that the specimen with 0.25 mm grain size and 50:50 weight proportions sustains a maximum load of 261.8 N with deflection of 2.5 mm.
From Fig. 10, it can be observed that the specimen with 0.25mm grain size and 60:40 weight proportions sustains a maximum load of 241.98 N with deflection of 2.94 mm. Hence, from these observations it is found that out of all weight proportions, the specimens with 0.25 mm grain size sustains maximum load when boiled at 40 °C.
Load v/s Deflection curves for the specimens boiled at 60 °C are as shown in Figures 11, 12 and 13.
From Fig. 11, it can be found that, the specimen with 0.25 mm grain size and 40:60 weight proportions upholds a maximum load of 248.52 N with deflection of 3.12 mm.
From Fig. 12, it can be observed that the specimen with 0.5 mm grain size and 50:50 weight proportions upholds a maximum load of 228.9 N with deflection of 2.896 mm.
From Fig. 13, it can be observed that the specimen with 0.25 mm grain size and 60:40 weight proportions upholds a maximum load of 235.44 N with deflection of 2.236 mm. Hence, from these observations it is found that out of all weight proportions, the specimens with 0.25 mm grain size withstands maximum load when boiled at 60 °C.
Load v/s Deflection curves for the specimens boiled at 80 °C are as shown in Figures 14, 15 and 16.
From Fig. 14, it can be observed that the specimen with 0.25 mm grain size and 40:60 weight proportions carries a maximum load of 241.98 N with deflection of 2.37 mm.
From Fig. 15, it can be observed that the specimen with 0.25 mm grain size and 50:50 weight proportions carries a maximum load of 215.82 N with deflection of 2.37 mm.
From Fig. 16, it can be observed that the specimen with0.25 mm grain size in 60:40 weight proportions carries a maximum load of 186.39 N with deflection of 1.63 mm. Hence, from these observations it is found that out of all weight proportions, the specimens with 0.25 mm grain size carries maximum load when boiled at 80 °C.
Analysis of flexural strength for the specimens boiled at different temperatures is shown in Figures 17, 18 and 19.
Table 1. Flexural strength of accelerated aged specimens boiled at different temperatures
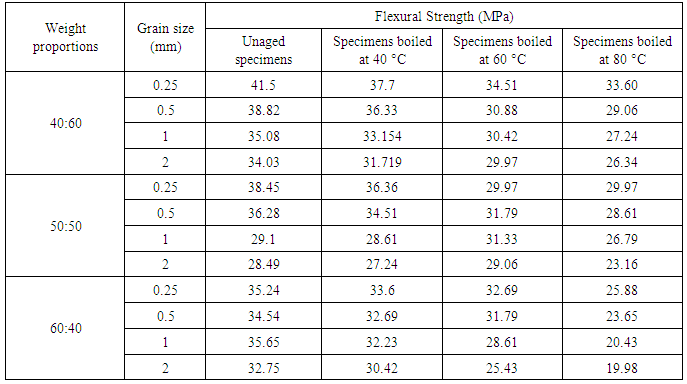
The flexural modulus is determined by taking the slope of load v/s deflection curves for all specimens. Analysis for flexural modulus for the specimens boiled at different temperatures is shown in Figures 20, 21 and 22.
Table 2. Flexural modulus of accelerated aged specimens boiled at different temperatures
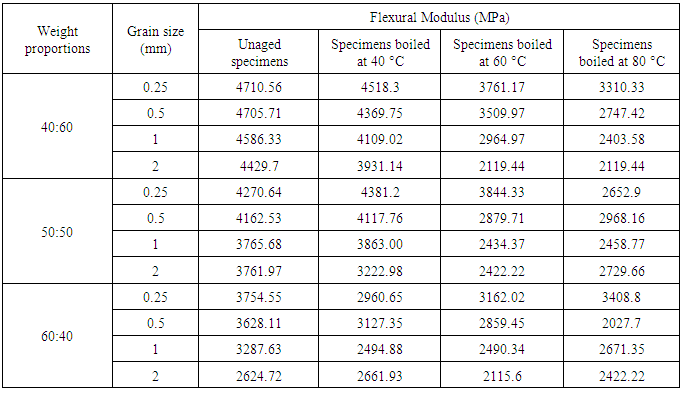
References
For further details log on website :
http://article.sapub.org/10.5923.c.materials.201502.26.html
ISSN: 2162-9382 e-ISSN: 2162-8424
2015; 5(3C): 126-132
doi:10.5923/c.materials.201502.26
Author
Sunil Kumar S. , Vinay D. R. , Saviraj A. S. , Prem Kumar Naik
Department of Mechanical Engineering, Mangalore Institute of Technology and Engineering, Moodabidri, Karnataka, India
Correspondence to: Sunil Kumar S. , Department of Mechanical Engineering, Mangalore Institute of Technology and Engineering, Moodabidri, Karnataka, India.
Email: | ![]() |
Copyright © 2015 Scientific & Academic Publishing. All Rights Reserved.
Abstract
This work deals with the study of flexural behavior of accelerated aged specimens of coconut shell epoxy composites. Three sets of specimens were subjected to hot boiling at temperatures of 40 °C, 60 °C and 80 °C respectively followed by the flexural test. Initially the coconut shells were cleaned, crushed, and sieved to different grain sizes of 0.25 mm, 0.5 mm, 1 mm and 2 mm. These grains were mixed with the epoxy resin with the weight proportions of 40:60, 50:50 and 60:40 (filler/resin weight proportions) and the composite boards were prepared by open mould process. The prepared specimens were cut according to the ASTM standards to carry out different tests. It was observed that the accelerated aged specimens of grain size 0.25 mm with weight proportion of 40:60 has higher flexural strength and flexural modulus with maximum deflection before failure compared to the specimens with other weight proportions.
Keywords: Accelerated ageing, Flexural test, Coconut shell/epoxy composites
Cite this paper: Sunil Kumar S. , Vinay D. R. , Saviraj A. S. , Prem Kumar Naik , Flexural Behaviour of Coconut Shell/Epoxy Composites Subjected to Accelerated Ageing, American Journal of Materials Science, Vol. 5 No. 3C, 2015, pp. 126-132. doi: 10.5923/c.materials.201502.26.
1. Introduction
Most commercially produced composites use a polymer matrix material often called a resin solution. There are many different polymers available depending upon the starting raw ingredients. There are several broad categories, each with numerous variations. The most common are known as polyester, vinyl ester, epoxy, phenolic, polyamide, polypropylene, polyether ether ketone (PEEK) and others. Polymer matrix composites are very popular due to their low cost and simple fabrication methods. Reinforcement of polymers by strong fibrous network permits fabrication of PMCs [1].
A particle by definition is non-fibrous and generally has no long dimension. The dimensions are approximately equal in all directions. The shape of the reinforcing particle may be spherical, cubic, platelet or any regular or irregular geometry. The arrangement of the particulate reinforcement may be random or with preferred orientation. Particles are effective in enhancing the stiffness of composites. The particles and matrix material in any particulate composites can be any combination of metallic and non-metallic materials [2]. Particulate fillers modify the physical and mechanical properties of polymers in many ways. The mechanical properties of particulate–polymer composites depend strongly on the particle size, particle–matrix interface adhesion and particle loading [3].
Coconut shell is one of the most important natural fillers produced in tropical countries. It is a natural lignocellulose material and possesses the distinctive characteristics that add to the versatility leading to diverse end uses such as- renewable resource, non toxic in nature, biodegradable, low density, low cost, easy availability and good durability [4]. Many works have been devoted to use of other natural fillers in composites in the recent past and coconut shell filler is a potential candidate for the development of new composites because of its high strength and modulus properties. Composites of high strength coconut filler can be used in the broad range of applications such as building materials, marine cordage, fishnets, furniture and other household appliances [5].
Physical aging is generally characterized by increase in mass density (volumetric relaxation) and/or decrease in molecular configurational energy (enthalpy relaxation) of materials when exposed to temperatures below the transition temperature [6].
2. Materials and Manufacturing
The raw materials used in this work are Coconut Shell Grains, Epoxy Resin (LY556), Hardener (HY951) and Melamine. Coconut shell grains were produced by crushing the coconut shells which is the most versatile part of the coconut. The shell is organic in nature and also has good durability characteristics, high toughness and abrasion resistant properties. The shell is similar to hard woods in chemical composition though lignin content is higher and cellulose content is lower. Advantages of natural fibers include low specific weight, which results in a higher specific strength and stiffness than glass. This is a benefit especially in parts designed for bending stiffness. Furthermore, it is a renewable resource, the production requires little energy and carbon dioxide is used while oxygen is given back to the atmosphere.
The shells of fully matured coconuts were first cleaned and crushed into smaller grains as shown in Fig. 2. These smaller grains were then subjected to repeated grinding in pulverizing machine, after passing through cyclones and vibratory sieves fitted with phosphor-bronze mesh, grains are finally drawn out in different mesh sizes.
![]() | Figure 1. Coconut Shells |
![]() | Figure 2. Coconut Shell grains |
2.1 Sieving Process
In this process, the coconut shell grains were sieved in to different grain sizes of 0.25 mm, 0.5 mm, 1mm and 2mm through the metallic sieves as shown in Fig. 3.
![]() | Figure 3. Sieved coconut shell grains of different sizes |
Open mould process was used to produce the composites. Initially the coconut shell particles of required grain sizes were weighed in a weighing machine, and then the required amount of epoxy resin, hardener and melamine powder were mixed with these grains and composites were produced.
The composite boards were prepared according to the following steps
Step 1: Appropriate volume of coconut shell particles and epoxy resin were taken in a plastic container and stirred thoroughly to make a homogeneous mixture. After adding 10% of hardener and 5% of melamine powder, the mixture was again stirred for 10 minutes.
Step 2: Open moulds used in this process were made from bright rod. Each mould has a cavity to accommodate the composite samples. The dimensions and shapes of cavities were made according to ASTM standards and thoroughly mixed mixture was poured in the mould.
Step 3: The composite samples were produced for different grain sizes of 0.25 mm, 0.5 mm, 1 mm and 2 mm.
![]() | Figure 4. Preparation of composite boards |
2.2 Flexural Test Specimens
Flexural strength is the ability of the composite material to withstand bending forces applied perpendicular to its longitudinal axis. Flexural test can be performed using 3-point bending method according to ASTM D790-03 standard procedure. The specimens are tested at a crosshead speed of 0.5 mm/min. The value of gauge length (L), width (d) and thickness (h) of the test specimen used in the experimentation are to be considered.
The specimens were prepared according to the ASTM D790-03 [7] with dimensions of the specimen in millimeter as 200 x 12 x 12 and the span length as 160 mm as shown in Fig. 5.
![]() | Figure 5. Flexural test specimen |
3. Experimentation
Accelerated aging is defined as the process or processes required to accelerate a specific mechanism or mechanisms relative to a baseline aging condition [8]. The specimens were subjected to accelerated ageing by hot boiling. Three sets of specimens of different grain sizes of 0.25 mm, 0.5 mm, 1 mm and 2 mm for different filler / resin weight proportions of 40:60, 50:50 and 60:40 respectively were boiled for three hours at different temperatures of 40 °C, 60 °C and 80 °C respectively for each set and then dried in the Oven for three hours at a temperature of 60 °C as shown in Fig. 6 [9].
![]() | Figure 6. Specimens subjected to hot boiling and kept in Furnace |
The flexural strength is calculated by [7, 10],
![]() | (1) |
The flexural modulus is determined by [7, 10],
![]() | (2) |
where,
P is maximum load in Newton
L is span length = 160 mm
b is width of specimen = 12 mm
h is thickness of specimen = 12 mm
m is slope of linear portion in load v/s deflection graph
The Flexural test was carried out in Universal Testing Machine (UTM) interfaced with deflectometer attachment as shown in the Fig. 7.
![]() | Figure 7. Specimen subjected to Flexural test in computer interfaced UTM with deflectometer set up |
4. Results and Discussion
The flexural strength and flexural modulus obtained for the specimens boiled at different temperatures are discussed below.
Load v/s Deflection curves for the specimens boiled at 40 °C are as shown in Figures 8, 9 and 10.
From Fig. 8, it can be observed that the specimen with 0.25 mm grain size and 40:60 weight proportions sustains a maximum load of 271.47 N with deflection of 4.3 mm.
![]() | Figure 8. Load v/s Deflection curves for 40:60 weight proportions |
From Fig. 9, it can be observed that the specimen with 0.25 mm grain size and 50:50 weight proportions sustains a maximum load of 261.8 N with deflection of 2.5 mm.
![]() | Figure 9. Load v/s Deflection curves for 50:50 weight proportions |
From Fig. 10, it can be observed that the specimen with 0.25mm grain size and 60:40 weight proportions sustains a maximum load of 241.98 N with deflection of 2.94 mm. Hence, from these observations it is found that out of all weight proportions, the specimens with 0.25 mm grain size sustains maximum load when boiled at 40 °C.
![]() | Figure 10. Load v/s Deflection curves for 60:40 weight proportions |
Load v/s Deflection curves for the specimens boiled at 60 °C are as shown in Figures 11, 12 and 13.
From Fig. 11, it can be found that, the specimen with 0.25 mm grain size and 40:60 weight proportions upholds a maximum load of 248.52 N with deflection of 3.12 mm.
![]() | Figure 11. Load v/s Deflection curves for 40:60 weight proportions |
From Fig. 12, it can be observed that the specimen with 0.5 mm grain size and 50:50 weight proportions upholds a maximum load of 228.9 N with deflection of 2.896 mm.
![]() | Figure 12. Load v/s Deflection curves for 50:50 weight proportions |
From Fig. 13, it can be observed that the specimen with 0.25 mm grain size and 60:40 weight proportions upholds a maximum load of 235.44 N with deflection of 2.236 mm. Hence, from these observations it is found that out of all weight proportions, the specimens with 0.25 mm grain size withstands maximum load when boiled at 60 °C.
![]() | Figure 13. Load v/s Deflection curves for 60:40 weight proportions |
Load v/s Deflection curves for the specimens boiled at 80 °C are as shown in Figures 14, 15 and 16.
From Fig. 14, it can be observed that the specimen with 0.25 mm grain size and 40:60 weight proportions carries a maximum load of 241.98 N with deflection of 2.37 mm.
![]() | Figure 14. Load v/s Deflection curves for 40:60 weight proportions |
From Fig. 15, it can be observed that the specimen with 0.25 mm grain size and 50:50 weight proportions carries a maximum load of 215.82 N with deflection of 2.37 mm.
![]() | Figure 15. Load v/s Deflection curves for 50:50 weight proportions |
From Fig. 16, it can be observed that the specimen with0.25 mm grain size in 60:40 weight proportions carries a maximum load of 186.39 N with deflection of 1.63 mm. Hence, from these observations it is found that out of all weight proportions, the specimens with 0.25 mm grain size carries maximum load when boiled at 80 °C.
![]() | Figure 16. Load v/s Deflection curves for 60:40 weight proportions |
Analysis of flexural strength for the specimens boiled at different temperatures is shown in Figures 17, 18 and 19.
![]() | Figure 17. Bar chart showing flexural strength for specimens boiled at 40 °C |
![]() | Figure 18. Bar chart showing flexural strength for specimens boiled at 60 °C |
![]() | Figure 19. Bar chart showing flexural strength for specimens boiled at 80 °C |
- From Table 1, the flexural strength of aged specimens has been found lesser than unaged specimens. Also, the decrease in the flexural strength has been found with increase in the size of grains and boiling temperature. From Figures 17, 18 & 19, it is clear that the specimen with 0.25 mm grain size and 40:60 weight proportion boiled at 40 °C is found to have higher flexural strength of 37.7 MPa.
Table 1. Flexural strength of accelerated aged specimens boiled at different temperatures
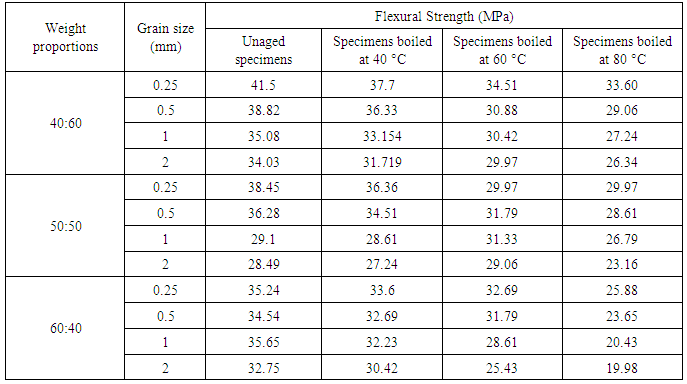
The flexural modulus is determined by taking the slope of load v/s deflection curves for all specimens. Analysis for flexural modulus for the specimens boiled at different temperatures is shown in Figures 20, 21 and 22.
![]() | Figure 20. Bar chart showing flexural modulus for specimens boiled at 40 °C |
![]() | Figure 21. Bar chart showing flexural modulus for specimens boiled at 60 °C |
![]() | Figure 22. Bar chart showing flexural modulus for specimens boiled at 80 °C |
- From Table 2 the flexural modulus of aged specimens is found lesser than unaged specimens. Also, the decrease in the flexural modulus is found with the increase in the grain size. From Figures 20, 21 & 22, the specimen with 0.25 mm grain size and 40:60 weight proportion boiled at 40 °C is found to have higher flexural modulus of 4518.3 MPa.
Table 2. Flexural modulus of accelerated aged specimens boiled at different temperatures
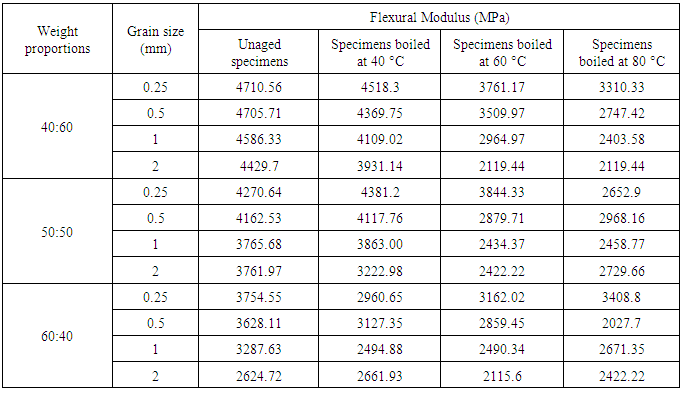
- The load v/s deflection curves for the specimens with 0.25 mm grain size out of all filler resin weight proportions are found to be smooth with maximum deflection at failure when compared to other grain sizes. This is because, the matrix adhesion of 0.25 mm grains is superior as compared to the rest and also the transformation of load throughout the material is uniform until failure. The specimens with filler resin weight proportion of 40:60 possess predominant values of deflection, flexural strength and flexural stiffness in comparison to rest of the specimens, the reason being the fact that the increase in resin proportion avoids the formation of voids during material processing.The comparison of the flexural behavior of accelerated aged specimens with that of unaged specimens depicts that the flexural strength and modulus of aged specimens are significantly lesser than that of unaged specimens. Both strength and modulus are found to be decreasing with increase in boiling temperature. The major reason for decreasing trend in flexural strength and modulus with increase in grain size and boiling temperature is that, the moisture causes degradation in the matrix and in turn reduces the bending stiffness of the polymer matrix composites. Also the increase in boiling temperature degrades interface between reinforcement and matrix system.
5. Conclusions
- The investigations carried out to determine the flexural stiffness of accelerated aged coconut shell particle epoxy composites divulge that the composites made of 0.25 mm grain size irrespective of weight proportions have higher flexural stiffness. It is also observed that the composites of 0.25 mm grain size and weight ratio 40:60 boiled at 40 °C have higher flexural strength of 37.7 MPa and flexural modulus of 4518.3 MPa. The review of the literature reveals that, the strength values of coconut shell particles are reasonably better than that of the composites made of fillers like groundnut shell particles, cocoa pod particles, wood dust particles such as teak wood, rubber wood etc. Since the coconut shell particles are abundant, cost effective, possess good strength and absorbs less water during hot boiling, it is an ideal reinforcement for making polymer matrix composite, which would be a substitute for wood-based materials and other applications.
References
For further details log on website :
http://article.sapub.org/10.5923.c.materials.201502.26.html
No comments:
Post a Comment