Author
By Jungle Boy
Bukit Nanas Forest Reserve (now called KL Forest Eco-Park) is a small patch of rainforest sited in the heart of Kuala Lumpur, at the base of the towering KL Tower, one of the tallest telecommunications structures in the world. Unknown to many, it is a small green patch that still preserves many species and features of the original rainforest that covered Kuala Lumpur at one time.
Although largely degraded from its original state, there are still some patches within that already tiny patch of forest that retain their original characteristics. Here the trees still stand tall, cicadas still buzz loudly all day long, and save for the sounds of the traffic outside, you would be forgiven for thinking you’re in the middle of an expansive wilderness.
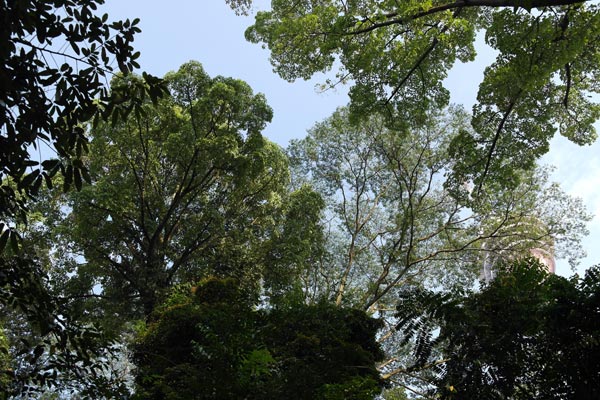
Nature and human edifice side by side. The Bukit Nanas Forest Reserve (KL Forest Eco-Park) still provides shelter for many trees, plants, and animals right in the heart of Kuala Lumpur city.
Background
Bukit Nanas Forest Reserve covers an area of 9.3 hectares. It was originally gazetted as a forest reserve way back in 1906 with a land area of 17.5 hectares, but since then, a large part has already been taken up for building the KL Tower and other purposes. The forest has long suffered from random logging, encroachment, and even war activities, so it’s quite a surprise to find some trees that appear to be several hundred years old in the forest itself.

Some impressively large trees still remain at Bukit Nanas. It is a relic patch of “primary” rainforest in a large metropolis, one of the few in the world, I believe.
During the early years of Kuala Lumpur’s formation, there were pitched battles between rival clans and warlords, and the forested hill was the site of a fort (nothing remains of it today) in the 19th century. According to historical accounts, pineapples (“nanas” in Malay) were planted all around the fort to deter attackers, hence the name Bukit Nanas (Pineapple Hill) today.
Back in the early 80s, the hill was the site of a small cable car project, but the whole project was scrapped soon after and the cable car service was shut down and dismantled. The forest has now been officially renamed as the KL Forest Eco-Park, but most KL citizens will still know and call it by its old name.
Trails in Bukit Nanas Forest Reserve
There are several trails that run through the forest reserve, which if seen from the air, is mainly limited to the one side of the hill, with the central portion or highest point taken up by the KL Tower. The official entrance is located near Jalan Raja Chulan, but the easiest way to get to the forest is by taking the Rapid KL LRT and disembarking at the Dang Wangi LRT Station.

Map of Bukit Nanas Forest Reserve, taken from one of the maps on display there. Click for larger view.
Continue from the Dang Wangi station by taking the overhead bridge across Jalan Ampang right in front of the station, and walking on in the direction of the KL Monorail Bukit Nanas Station. A short distance ahead, you will encounter a small gallery, Wariseni, and behind this gallery is a footpath into the Bukit Nanas Forest Reserve, taking you up the hill through a long flight of stairs. Climbing up can be a little tiring, so take your time.

The long flight of stairs up the hill takes you into the forest park.

The Jelutong Trail.
The first trail you can see branches off from this footpath, with its name clearly signposted – Jelutong Trail. This looping trail skirts the side of the reserve and the lower half of it is currently overgrown. However, the top half of the trail is still fine, and takes you past some large trees. Most of them are labeled with some information about them on wooden plaques mounted on pedestals. It soon becomes obvious why the trail is so named; jelutong (Dyera costulata) trees are obvious along the trail, and you will pass a huge jelutong tree if you continue along to the end (or start, if coming from the other direction) of the trail.

The big Jelutong (Dyera costulata) tree found by the side of the Jelutong Trail.

Surian Wangi (Toona sureni) tree with nice buttress roots. Many of the trees at Bukit Nanas are labeled, making it a great place for nature education.

Bamboo Walk, a pleasant stretch flanked by clumps of giant bamboo.
The Jelutong Trail allows you to cross onto the Bamboo Walk, a tiled pavement with huge bamboo clumps growing on the sides. Walking straight on the Bamboo Walk takes you through an old banana grove, where you can detour down to the Suboh Trail, a picturesque trail passing through the banana plantation. It takes you right to the edge of the forest reserve, bordering the Convent school, and ends at a small tarred road called Jalan Aquilaria that connects to Jalan Bukit Nanas.

Suboh Trail, a path set amongst banana trees, which changes to typical rainforest later on.
If you skip the Jelutong Trail and continue along the concrete stairway, you will pass a small built-up area to do calisthenics, with various apparatus as well. Continuing on will take you across a wooden bridge and onto a wide open “activities” area. It may be possible to camp here (with permission from the Forest Department). Right ahead, the KL Tower looms.

Wooden plank walkway at Bukit Nanas, which allows for observation of the surrounding rainforest understory.
Walking to the end of this open area leads you back into the forest. Here, you have a choice between taking the Merawan Trail, or the short plank walkway built over the forest floor. Both are interesting and short, so why not both? The former is another jungle trail that takes you past a few large trees like the Merawan Batu (Hopea beccariana), a dipterocarp, and a big Pulai tree (Alstonia angustiloba). The latter gives you a good picture of the understory structure of a typical Malayan rainforest, without having to get your feet dirty and passes one of the few patches in the forest reserve that still has an intact canopy.

The Merawan Trail is perhaps the quietest trail in the park. It is farthest from the outward city-facing edge of the forest, and traverses some nooks and crannies.

Merawan Batu (Hopea beccariana), found along the Merawan trail.

Large Pulai tree (Alstonia angustiloba), and the KL Tower, in view. Pulai is a common wayside/secondary forest tree in Malaysia, but they are usually not large. Here however, they are able to grow old and big.
If you take the Merawan Trail, it ends at a stairway and across it, the Penarahan Trail awaits, another short trail passing through a patch with more or less intact canopy (and rainforest structure). This trail is notable for having some unique, twisting lianas.

Penarahan Trail, a nice trail with some twisting lianas to be found.

The “undisturbed” rainforest of Bukit Nanas, as seen from the Penarahan Trail. Note the large liana.

Looking like a thick twisty rope, this climbing liana/vine coils around the tall trees to reach into the canopy and sunlight.
The Information Centre is located just off Jalan Raja Chulan and has a small exhibit with some old photos and information. Behind the Information Centre is a Herbal Garden exhibiting a variety of local herbs, an Orchid Garden, and an Arboretum Trail nearby. At the time of this writing, construction of some sort of cable car or canopy “skywalk” was ongoing (and has been going on for the past 1.5 years at least). If and when it is finally opened, it should be an added attraction in addition to the KL Tower, just a stone’s throw away. [Latest update – The Skywalk at Bukit Nanas is now open. It features a long walkway anchored by towers at up to about 20m above ground, and links the rear of the Information Center with the KL Tower entrance.]

The Bukit Nanas Skywalk

Inside the Bukit Nanas/KL Forest Eco-Park Information Center.

The Herbal Garden has some common and less common Malaysian herbs.
Wildlife
Someone relocated a troupe of silvered leaf monkeys (Trachypithecus cristatus) into the forest here; normally these monkeys are denizens of coastal/estuary forests, so I am not entirely sure if they can survive long term in this tiny forest. Here, they are totally unafraid of humans, so it may be they were relocated from the Kuala Selangor/Bukit Melawati area with its burgeoning population of silvered leaf monkeys.

KL Forest Eco-Park is home to perhaps 20 or so silvered leaf monkeys that were likely trans-located here. Notice the color of their young is very different from the adults.
Other than squirrels, skinks, snakes, small reptiles, some species of birds, and of course, numerous invertebrates, there doesn’t seem to be any other native wildlife remaining in this tiny green island surrounded by concrete jungle. There might be long tailed macaques (Macaca fascicularis), but I did not encounter any despite several trips here.

Large Batai (Paraserianthes falcataria) trees grow here at Bukit Nanas. These fast growing trees are not native to Malaysia, but those at Bukit Nanas are old due to being planted/established many years ago.
Summary
While I wouldn’t say the Bukit Nanas Forest Reserve/KL Forest Eco Park is a perfect example of what an undisturbed Malaysian tropical lowland rainforest ought to be, it is still a welcome respite from the stressful KL life, and a much needed green lung smack right in the middle of the city. It also presents an opportunity to study the changes that affect an isolated island of “primary” rainforest over a sustained period of time, especially with introduced species (some of the old trees appear to be planted or introduced here).
For a casual visit, it can be a pleasant place to enjoy nature, but due to its disturbed character/surroundings, mosquitoes can be quite common during wet weather, so mosquito repellant should come in handy here. Visiting hours are from 8 am to 5 pm daily.
For further information log on website :
https://www.rainforestjournal.com/a-walk-through-the-bukit-nanas-forest-reserve/